At Keurig Dr Pepper, our reputation for breaking boundaries shapes careers. We think boldly and deliver with confidence. And we do it all, together. Be part of a collaborative culture that gives you a real chance to influence iconic brands – and have fun doing it. Learn more about our 28,000-strong team, and a celebrated company that’s just getting started. Drink in the possibilities.
Explore our career areas
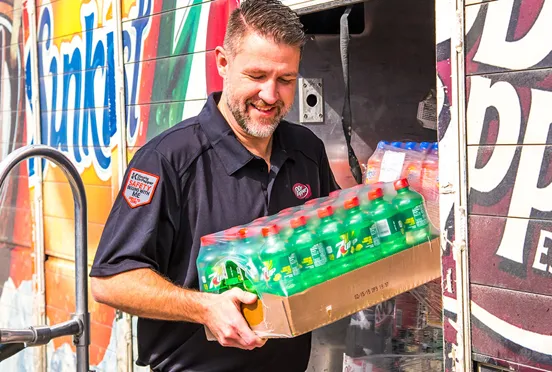
Merchandisers
Use your people skills in stores to keep our products on shelves.
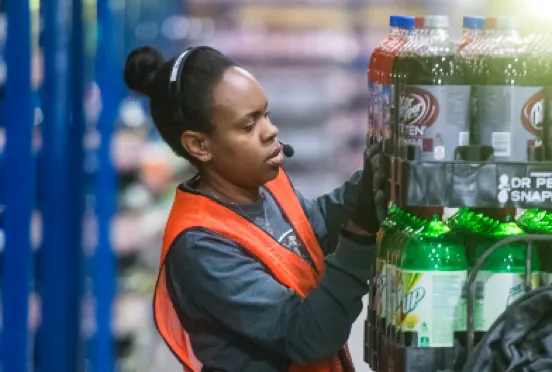
Warehouse
Make sure our products are ready to go in one of these crucial roles.
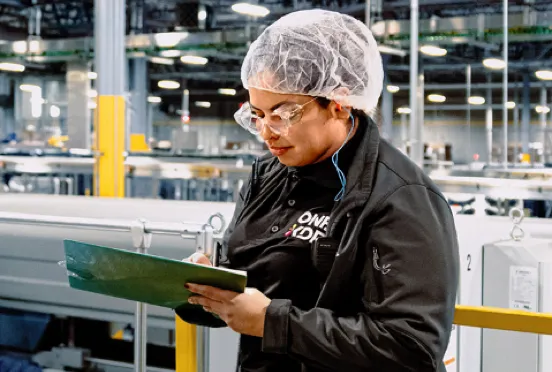
Supply Chain
Build your career in a fast-moving area with room to grow.
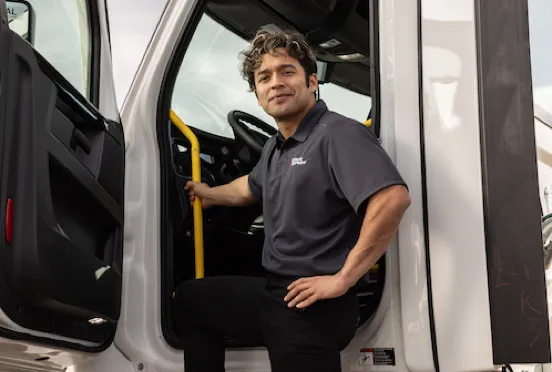
Drivers
Keep our products moving as the face of our company.
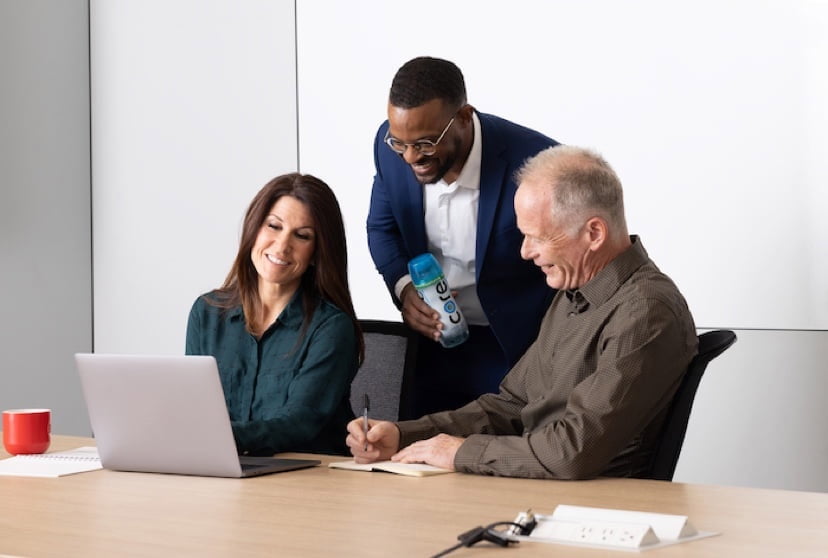
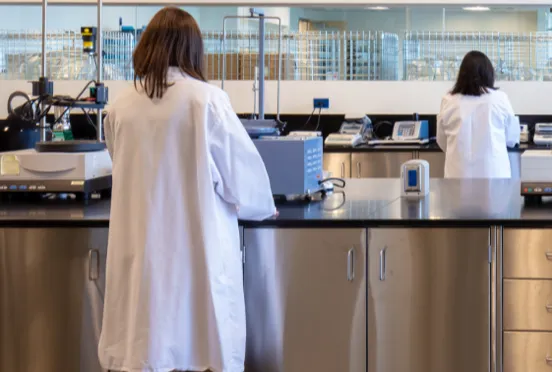
Technology
Solve impactful and exciting tech challenges.
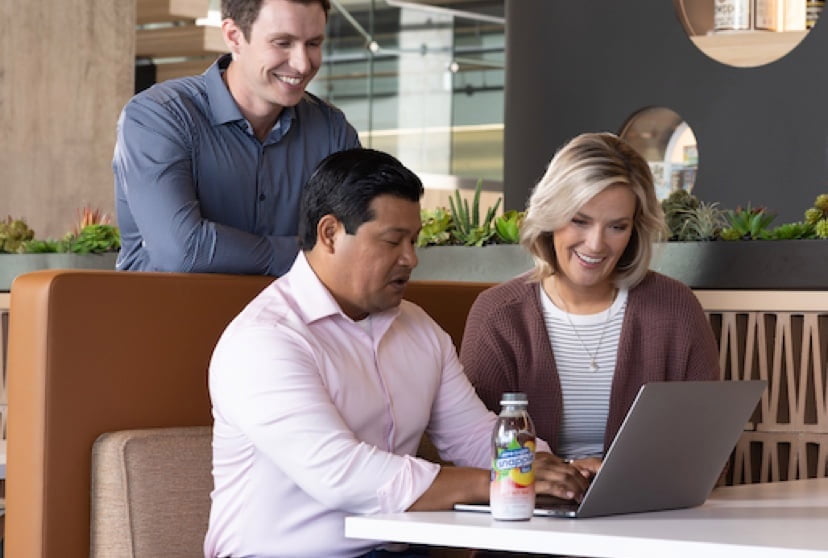
Corporate
Support the growth of our business and shape an industry.
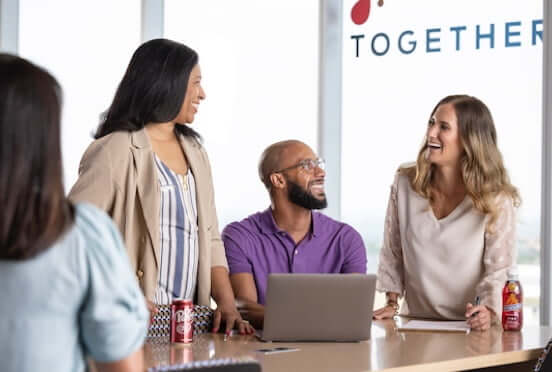
Connect with who we are
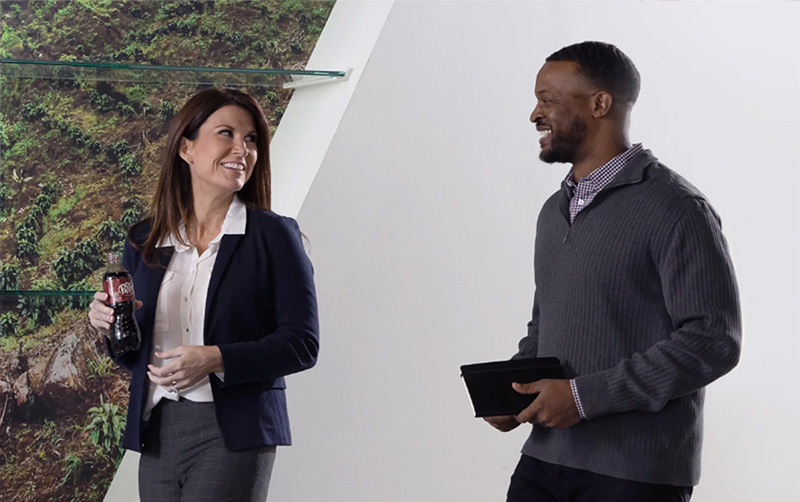
Find your place on our collaborative team
To chart a new path in the beverage industry, it takes people with a refreshing combination of vision and passion. Our team brings together a wide variety of experience, skills, and perspectives to seize opportunities and build a sustainable future, together. Find out more about our team-first culture that brings out the best in everyone.
Learn More about our collaborative teamExperience an award-winning culture
Get to know our brands
Challenge the usual with distinctive brands
You’re ready to grab hold of big, bold opportunity, and you’ll find it everywhere you look at KDP. Our owned, licensed, and partner brands include some of the most popular and well-respected names in beverages – and beyond. Learn more about our 125+ brands and begin your future full of possibility as part of our team.
Explore Our Brands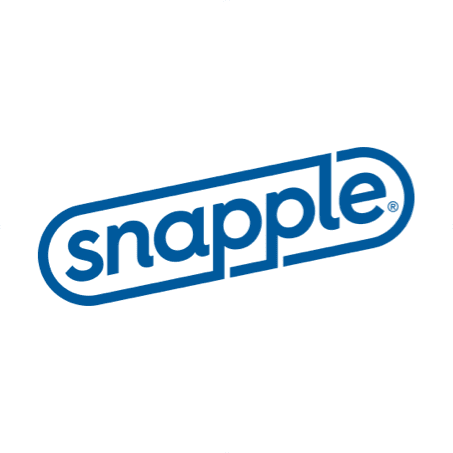
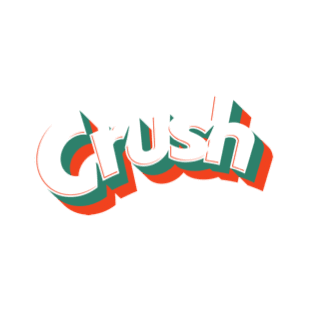
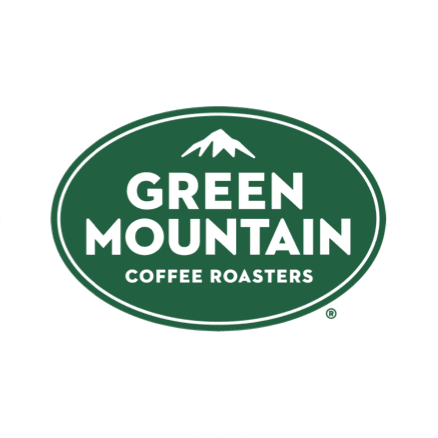
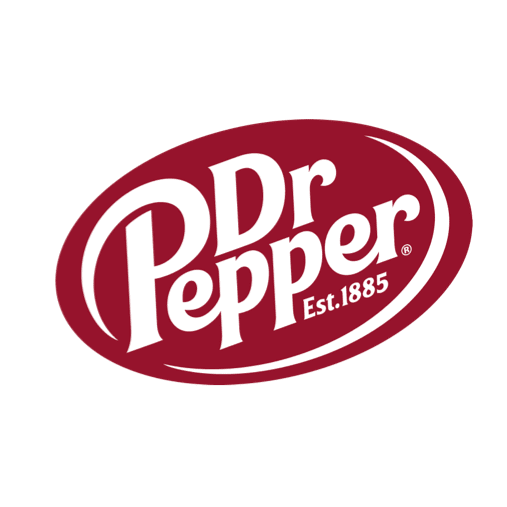
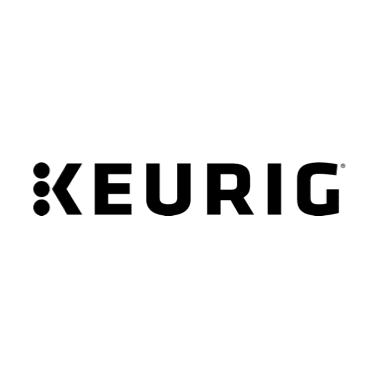
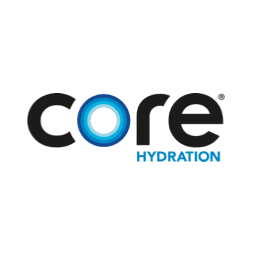
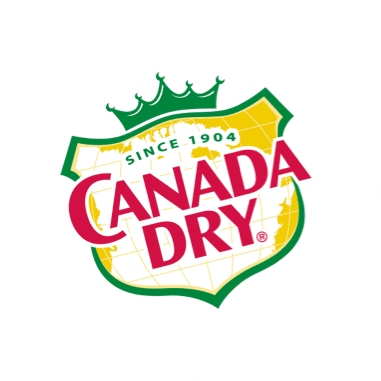
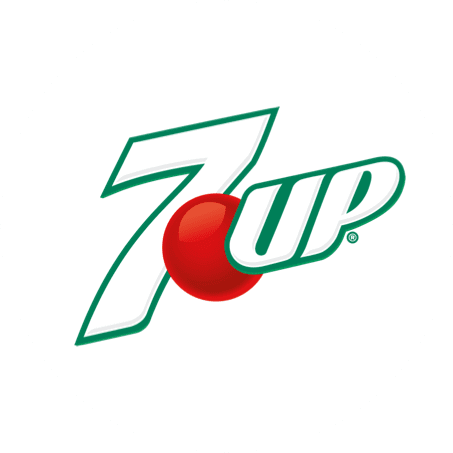